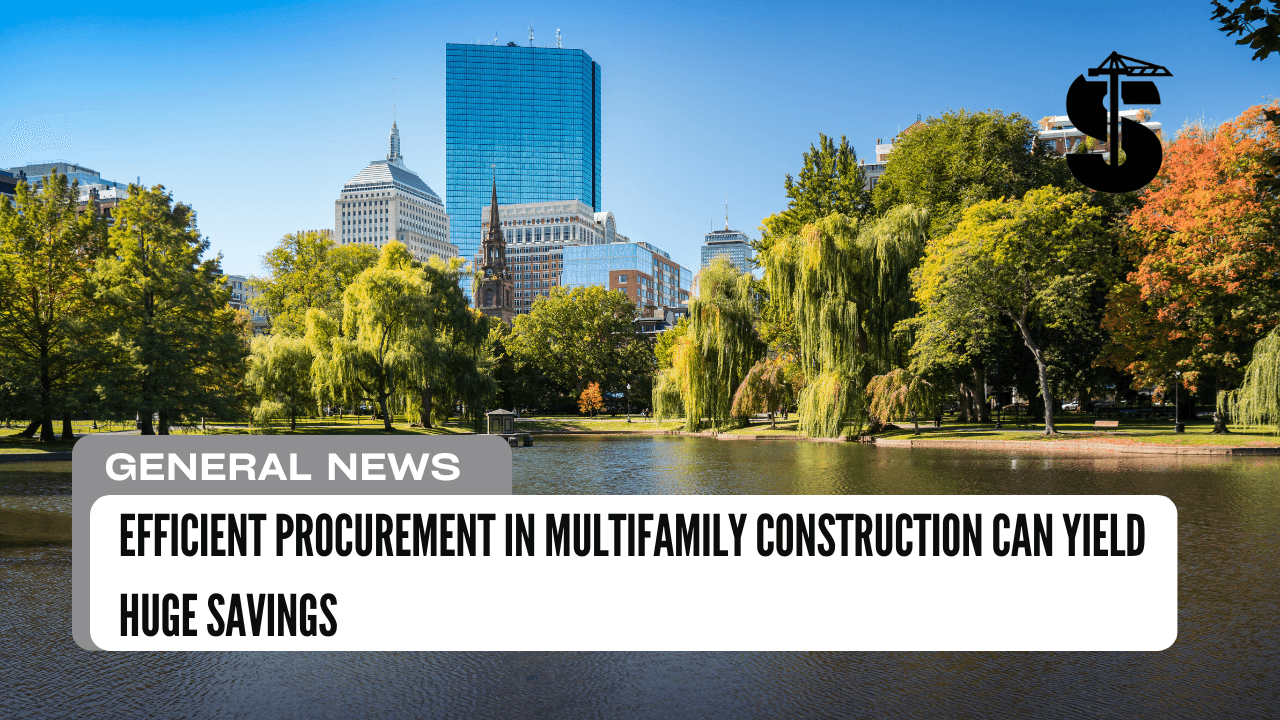
Efficient Procurement in Multifamily Construction Can Yield Huge Savings
Key Highlights:
- Industrialized construction can significantly reduce costs in concrete, insurance, and construction-loan interest rates.
- Collaboration with specialty firms for procurement and prefabrication is crucial.
- Precision and close coordination among the AEC team are essential for success.
- Insurance premiums can be lowered due to noncombustible materials used in industrialized construction.
- Accelerated schedules can save up to $40,000 for every $1 million financed in carry costs.
Source (PR Newswire)
Quotes
“ "Industrialized construction also centers on the aggregated benefits of taking an upstream approach to the supply chain. Because those prefab steel studs are classified as noncombustible, the project's insurance premiums are a fraction of those associated with conventional, stick-framed construction. The developer's single procurement contact relies on strong relationships with suppliers of standardized equipment to source project components with shorter lead times and deliver and install them faster." ”
Aksel Solberg, AIA, NCARB, Leader of Development Design Studio at HFA Architecture + Engineering
Our Take:
Adopting industrialized construction methods presents a compelling case for multifamily developers seeking to optimize costs and schedules. By collaborating with specialty firms like ICS, developers can leverage the efficiency of prefabrication while maintaining precision and coordination across the project lifecycle. The substantial savings in insurance premiums and construction-loan interest rates, combined with the predictability of costs and schedules, underscore the transformative potential of industrialized construction in the multifamily sector. Initiating conversations with AEC teams about these innovative approaches could be a strategic move for developers aiming to enhance their project's efficiency and profitability.